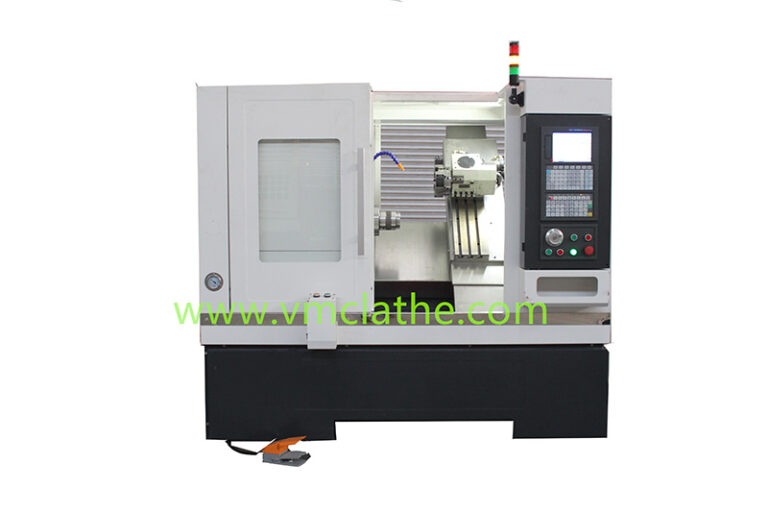
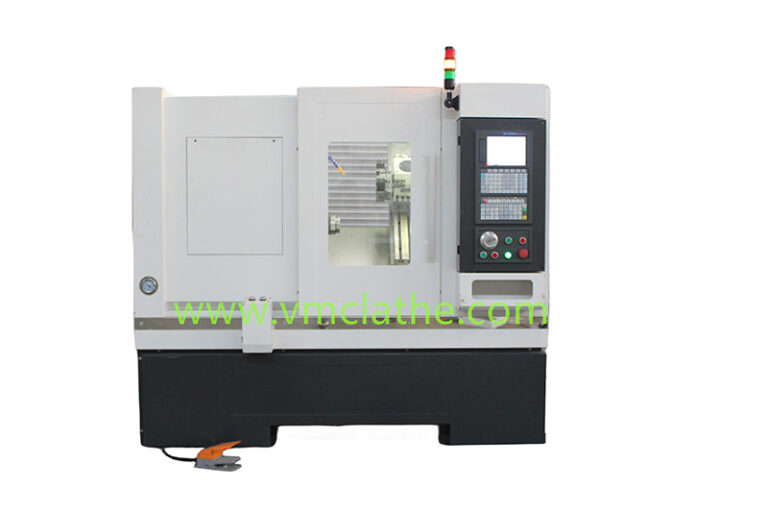
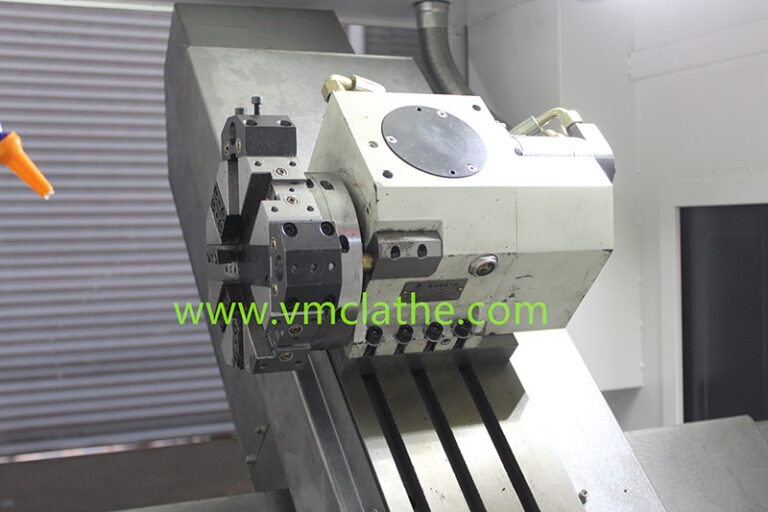
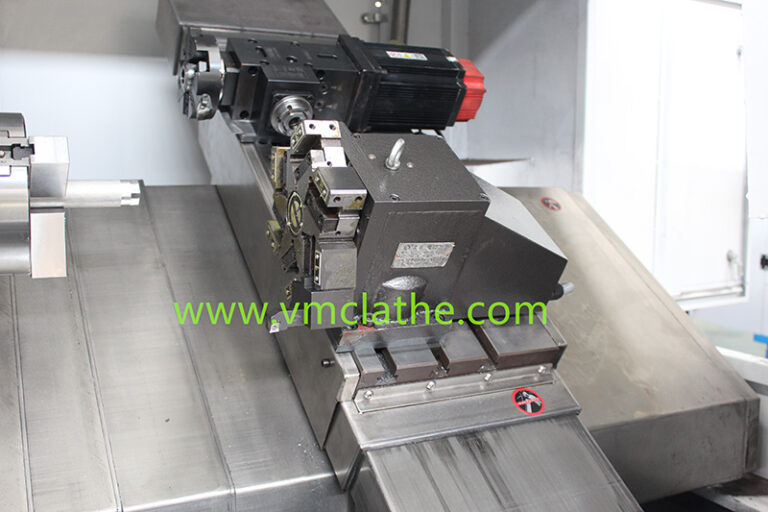
TCK40M CNC Lathe Machine Large Slant Bed CNC with Live Tool
China Manufacturer direct supply high precision TCK40M slant bed cnc lathe machine
CNC lathe live tooling metal processing working cnc slant bed lathe made in China
Slant bed cnc lathe machine TCK40M
ITM | UNIT | TCK40M |
Max. swing dia. over bed | mm | 400 |
Max. swing dia. over slide | mm | 150 |
Max. cutting dia. Of disc type parts | mm | 300 |
Max. cutting dia. Of axle type parts | mm | 130 |
X axis travel | mm | 620 |
Z axis travel | mm | 360 |
Max. process length | Mm | 200 |
X Z Fast feed | mm/min | 12000 |
spindle bore | mm | 48 |
through hole bar diameter | Mm | 42 |
spindle nose type | A2-5 | |
spindle speed | rpm | 3000 |
main motor power | kw | 4 |
positioning accuracy | mm | 0.012 |
XZ repeatability | mm | 0.003 |
Diameter uniformity | mm | 0.03/300 |
Flatness | mm | 0.03/200 |
tool post type | Gang tool/8 hydraulic turret | |
tailstock | No tailstock | |
Dia. of tailstock sleeve | Mm | |
Tailstock sleeve taper | ||
Chuck | Hydraulic collet/6inch hydraulic chuck | |
bed inclination | 45 degree | |
size | ||
weight |
Get Free Quote of TCK40M
Related Products
Related News
The multi-axis linkage technology of slant bed CNC lathe is a key technology for complex parts processing in modern manufacturing. The following is a detailed introduction for you: 1. Principle of multi-axis linkage technology Multi-axis linkage refers to the precise position and posture control of the tool relative to the workpiece in space through the […]
The configuration selection of slant bed CNC lathe will directly affect its processing performance and scope of application. The following is an introduction to configuration selection from entry-level to high-end: 1. Entry-level configuration A. Control system: You can choose control systems such as GSK. This type of system has a simple operation interface, relatively simple […]
The five key factors in purchasing a CNC lathe with an inclined bed are as follows: Processing requirement matching A. Part type: Make it clear whether the parts to be processed are shafts, discs or other complex shapes. If there are many shaft parts to be processed, it is necessary to pay attention to whether […]
Precise thread processing on a slant bed CNC lathe requires a series of rigorous operating steps and precautions. Here are some key points: 1. Tool selection and preparation A. Tool type: Select appropriate tools such as taps, thread milling cutters or thread turning tools according to the form and processing method of the thread. Make […]
Compared with traditional flat bed CNC lathes, slant bed CNC lathes have significant technical advantages. The following are the five technical advantages of slant bed CNC lathes 1. High precision: A. Slant bed CNC lathes use high-precision ball screws and linear guides to ensure the positioning accuracy and repeat positioning accuracy of the machine tool […]
Choosing a slant bed CNC lathe with powered toolholder is a wise move to improve processing efficiency and precision. Here are five reasons to choose this type of lathe: 1. High-precision processing capability: 1) The slant bed design itself provides higher rigidity and stability, reduces vibration, and thus ensures high precision during processing. 2) The […]
Slant-bed CNC lathes have shown significant technical advantages in complex parts processing and have been widely used. The following is a specific analysis of its technical advantages and applications: 1. Technical advantages 1) Structural advantages a) Slant bed design: The bed of the slant-bed CNC lathe is designed at an angle. This structure can more […]
The practical application of the power turret in the inclined bed CNC lathe is mainly reflected in the following aspects: 1. Improve processing efficiency: The power turret itself has a power source and can independently provide the main motion and feed motion to the tool to complete milling, drilling, and mantis processing. This independence enables […]
The debugging tips for the Y-axis of a slant-bed CNC lathe are essential for improving machining accuracy. Here are some specific debugging tips and strategies to help optimize the performance and machining accuracy of the Y-axis: Mechanical adjustment and maintenance: o Y-axis guideway inspection: Ensure that the straightness, horizontality, and parallelism of the Y-axis guideway […]