Maintenance and inspection of mechanical parts of CNC milling machine processing center are the key to ensure long-term stable operation of equipment, improve processing accuracy and extend service life. The following are detailed maintenance and inspection points, which are explained in steps:
1. Daily maintenance and inspection
A. Cleaning work
a) Machine surface: After processing every day, wipe the machine shell, operation panel, and display screen with a clean cloth to avoid oil and dust accumulation.
b) Workbench and guide rails: Remove chips and coolant residue to prevent rust and scratches. Use a special scraper or vacuum cleaner to clean the debris in the guide rail groove.
c) Tool magazine and tool change mechanism: Check whether the tool handle and tool claw are clean to avoid chip jamming and tool change failure.
B. Lubrication system inspection
a) Guide rail and screw lubrication: Confirm whether the oil level of the automatic lubrication pump is normal, and the manual lubrication points need to be regularly filled with specified grease (such as lithium-based grease).
b) Oil circuit patency: Check whether the lubrication pipeline is leaking or blocked, and ensure that the lubricating oil can be evenly distributed to the guide rails, lead screws and other parts.
C. Coolant management
a) Liquid level and concentration: Check the coolant level and replenish it in time; regularly check the concentration (usually 5%-10%) to prevent corruption.
b) Filter cleaning: Clean or replace the coolant filter to prevent impurities from clogging the nozzle.
D. Air pressure system inspection
a) Air pressure value: Confirm whether the pressure of the barometer is stable (usually 0.4-0.6MPa), and check whether the air pipe has air leaks.
b) Air source treatment: Empty the accumulated water in the air filter to prevent moisture from entering the spindle or tool magazine.
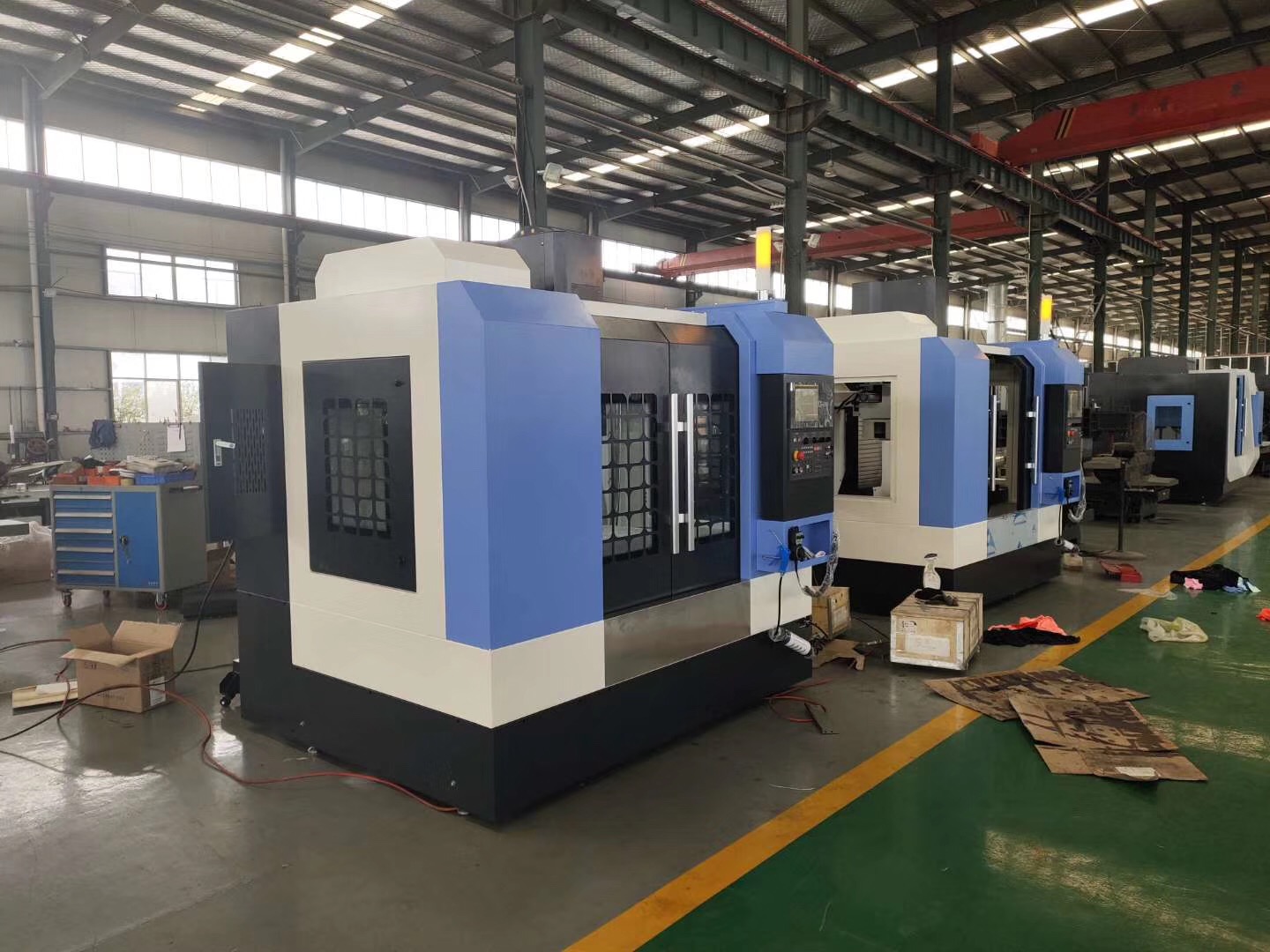
2. Weekly/monthly maintenance
A. Mechanical parts inspection
a) Guide rails and lead screws: Check for wear, scratches or increased clearance, and move each axis in manual mode to listen for abnormal noise.
b) Bearings and spindles: Check whether the spindle runs smoothly and whether the temperature rise is normal (generally ≤60℃). Re-tighten the bearings if necessary.
c) Belts and couplings: Check the belt tension (press the midpoint with your finger, the sag is about 10mm), and whether the coupling is loose.
B. Bolts and fasteners
a) Use a torque wrench to check whether the bolts of various parts (such as the workbench, spindle box, motor seat) are loose, especially high-speed moving parts.
C. Chip removal system
a) Clean the chip conveyor chain and scraper, check whether the motor runs normally, and avoid chip accumulation and jamming.
3. Quarterly/annual in-depth maintenance
A. Accuracy detection and calibration
a) Geometric accuracy: Use a dial indicator and laser interferometer to detect the positioning accuracy and repeat positioning accuracy of each axis (such as ISO 230-2 standard).
b) Spindle runout: Use a micrometer to measure the radial/axial runout of the spindle (usually required to be ≤0.005mm).
c) Backlash compensation: Use the ballbar to detect and adjust the backlash parameters of the CNC system.
B. Hydraulic/pneumatic system maintenance
a) Replace the hydraulic oil (recommended once a year), clean the oil tank; check whether the cylinder seal is aging.
C. Electrical component inspection
a) Clean the dust in the electric cabinet, check whether the relay and contactor contacts are burned; whether the servo motor cooling fan is normal.
D. Protective device
a) Check the function of the protective cover and door switch to ensure that the safety interlock is effective; clean the chips in the guide rail protective cover.
4. Special maintenance of key components
A. Spindle maintenance
a) Regular lubrication: For non-electric spindles, replace the grease according to the manual requirements (such as every 2000 hours).
b) Cooling system: Check whether the cooling channel in the spindle is unobstructed, and the water-cooled spindle needs to be anti-freezing and anti-scaling.
B. Tool magazine maintenance
a) Robot maintenance: Clean the claw spring mechanism and apply grease; check whether the tool change position is accurate.
b) Tool holder cleaning: Wipe the tool holder cone with alcohol regularly to prevent dirt from affecting positioning accuracy.
C. Ball screw
a) Remove the protective cover to clean the old grease, and reapply special grease for high-speed screws (such as Shell Gadus S2).
5. Notes
A. Use original consumables: Lubricating oil, hydraulic oil, etc. must comply with the requirements of the equipment manual.
B. Record maintenance log: Record the time, content and abnormal conditions after each maintenance to facilitate problem tracking.
C. Abnormal handling: Stop the machine immediately for investigation when vibration, abnormal sound or reduced accuracy is found to avoid the expansion of faults.
Through a systematic maintenance plan, the failure rate of CNC milling machines can be significantly reduced. It is recommended to formulate a personalized maintenance cycle in combination with the equipment manual and actual working conditions (such as shortening the maintenance interval for high-load processing).